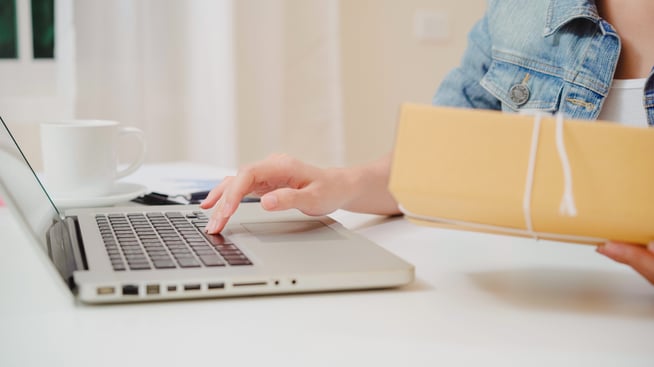
Today, we're delving into the world of Assembly Items that come with special order inventory components. Essentially, this means that within the Bill of Materials, one of the inventory items is a special order item. The catch here is that this special-order item isn't stocked at your current location. Now, it's important to clarify the distinction between special orders and drop shipments. While a drop shipment involves the item being shipped directly to the customer, a special-order item is received at your company's warehouse first. However, don't forget, you still have the flexibility to switch to a drop shipment on the line level field if the need arises.
When you're in the process of creating the Bill of Materials for your Assembly Item and adding various components, you get to decide where these components will come from. Are you pulling them from your current inventory stock, or are they coming from purchase orders that you're placing, which will then be assigned to the assembly upon receipt? When you add an inventory item with the Special Order feature enabled, you'll notice that the item source is automatically set to "Purchase Order."
Take a look at the screenshot above, and you'll see that 'Dummy Inv Item 2' has the special-order feature enabled on its item record, and the source is automatically set to "Purchase Order." This means that when creating a Sales Order with this assembly item, you have two ordering and building options. Let's walk through these options.
Option 1:
Here's how it works:
- Sales Order - You initiate the process by creating a Sales Order.
- Creates Work Order - Within the Sales Order, you have the option to select the "Create WO" checkbox. This action triggers NetSuite to automatically create a corresponding Work Order for that item.
- Release Work Order - After creating the Work Order, you can change its status from "Planned" to "Release." This triggers the creation of a Purchase Order.
- Creates Purchase Order - Since this item was set as a special-order item, the Purchase Order is generated specifically to receive this item from the preferred vendor for this order.
- Receive Purchase Order - Once the Purchase Order is created, you can receive the item once it arrives at your warehouse.
- Build Assembly - After receiving the item, you can go back to the Work Order and build the assembly since all components are now available. Simply select "Create Build" on the Work Order record.
- Fulfillment on Sales Order - Finally, with the item built, you can return to the Sales Order and fulfill it as you would with any other order.
This is your first option when using special-order items as components in an assembly.
Option 2:
Here's the second option:
- Sales Order - You begin by creating a Sales Order.
- Purchase Order - Unlike the first option, you won't check the "Create Work Order" field. Leave it unchecked. The Purchase Order for the special-order item will be generated after saving the Sales Order.
- Receive Purchase Order - Once the Purchase Order is created, you'll receive the item when it arrives at your warehouse.
- Create Assembly Build - Now that the components are in stock, you can create an assembly build.
- Fulfillment - After building the assembly, return to the Sales Order and fulfill it as usual.
So, what's the difference between these two options? Well, it primarily comes down to the number of records and your preference for traceability. Option one allows you to generate a Work Order, providing detailed records of each step in the process. On the other hand, option two skips this entirely, and users proceed directly to the assembly build since all required items are in stock. This simplifies the process but removes some of the detailed traceability provided by the first option.
In essence, NetSuite equips you with the flexibility to create assembly items with special-order components, a valuable tool when these components aren't readily available in your current inventory stock. If you have any questions or would like to see this process in action, please don't hesitate to reach out to our team. We're here to help!
About Us
Concentrus is a leading provider of innovative cloud-based enterprise resource planning (ERP) solutions, including NetSuite. Our team of NetSuite experts offers a range of services, including NetSuite price analysis, NetSuite training, and NetSuite integration services.
Our goal is to help businesses of all sizes maximize their investment in NetSuite by providing expert NetSuite cost optimization and implementation strategies. With years of experience as a NetSuite partner, our NetSuite administrators and NetSuite consultants are well equipped to help businesses of all sizes with their NetSuite consulting needs.
Whether you're looking for a NetSuite consultant to help with your NetSuite implementation or you need ongoing NetSuite support, Concentrus is here to help.
Read About Our Implementation Methodology
Want more NetSuite Tips and Tricks? Check out our Short & 'Suite videos